Underwater Welding
Knowledge Corridor, Raisan, Gandhinagar-382007,Gujarat. Underwater Welding. INTRODUCTION.
Share Presentation
Embed Code
Link
Download Presentation
- welding
- wet welding
- hyperbaric welding
- arc welding
- wet underwater welding
- gas tungsten arc welding

fhebert + Follow
Download Presentation
Underwater Welding
An Image/Link below is provided (as is) to download presentation Download Policy: Content on the Website is provided to you AS IS for your information and personal use and may not be sold / licensed / shared on other websites without getting consent from its author. Content is provided to you AS IS for your information and personal use only. Download presentation by click this link. While downloading, if for some reason you are not able to download a presentation, the publisher may have deleted the file from their server. During download, if you can't get a presentation, the file might be deleted by the publisher.
Presentation Transcript
- Knowledge Corridor, Raisan, Gandhinagar-382007,Gujarat Underwater Welding
- INTRODUCTION
- • The fact that electric arc could operate wasknown for over a 100 years. The first everunderwater welding was carried out by BritishAdmiralty - Dockyard for sealing leaking shiprivets below the water line. • Underwater welding is an important tool forunderwater fabrication works. • In 1946, special waterproof electrodes weredeveloped in Holland by ‘Van der Willingen’.
- CONTD. • In recent years the number of offshore structures including oil drilling rigs, pipelines,platforms are being installed significantly. • Some of these structures will experience failuresof its elements during normal usage and duringunpredicted occurrences like storms, collisions.Any repair method will require the use ofunderwater welding.
- CONTD. • Underwater welding is the process of weldingat elevated pressures, normallyunderwater. Underwater weldingcan either take place wet in the water itself or dry inside a specially constructed positive pressure enclosure and hence adry environment. It is predominantly referred to as"hyperbaric welding" when used in a dry environment, and"underwater welding" when in a wet environment • The applications of underwater welding are diverse—it is oftenused to repair ships, offshore oil platforms, and pipelines. Steel is the most common material welded.
- CONTD. • Dry hyperbaric welding is used in preference to wet underwater welding when high quality welds are required because of the increased control over conditions which can beexerted, such as through applicant of prior and postweld heat treatments • This improved environmental control leads directly to improved process performance and a generally much higherquality weld than a comparative wet weld. Thus, when a veryhigh quality weld is required, dry hyperbaric welding isnormally utilized.
- CONTD. •Research into using dry hyperbaric welding at depths of up to1,000 metres (3,300 e) is ongoing. In general, assuring theintegrity of underwater welds can be difficult (but is possibleusing various non-destructive testing applications), especiallyfor wet underwater welds, because defects are difficult todetect if the defects are beneath the surface of the weld.
- Classification 1. Dry 2. wet
- DRY WELDING • Dry hyperbaric welding involves the weld beingperformed at the prevailing pressure in achamber filled with a gas mixture sealed aroundthe structure being welded. • Most welding processes SMAW, FCAW, GTAW,GMAW, PAW could be operated at hyperbaricpressures, but all suffer as the pressureincreases. Gas tungsten arc welding is mostcommonly used.
- CONTD. • The degradation is associated with physical changes of the arc behavior as the gas flow regime around the arc changes and the arc rootscontract and become more mobile. • Of note is a dramatic increase in arc voltage which is associated with the increase in pressure. Overall a degradation in capability andefficiency results as the pressure increases.
- • Although, a large number of techniques areavailable for welding in atmosphere, many ofthese techniques can not be applied in offshoreand marine application where presence of wateris of major concern. • In this regard, it is relevant to note that, a greatmajority of offshore repairing and surfacing workis carried out at a relatively shallow depth, in theregion intermittently covered by the waterknown as the splash zone.
- CONTD. • Though, numerically most ship repair and welding jobsare carried out at a shallow depth, most technologicallychallenging task lies in the repairing at a deeper waterlevel, especially, in pipelines and occurrence/creation ofsudden defects leading to a catastrophic accidentalfailure. • The advantages of underwater welding are of economical nature, because underwater-welding for marine maintenance and repair jobs bypasses the needto pull the structure out of the sea and saves valuabletime and dry docking costs.
- • Special control techniques have been applied which have allowed welding down to 2500m simulated water depth in the laboratory, but dryhyperbaric welding has thus far been limitedoperationally to less than 400m water depth bythe physiological capability of divers to operatethe welding equipment at high pressures andpractical considerations concerning constructionof an automated pressure / welding chamber atdepth
- ADVANTAGES 1) Welder/Diver Safety - Welding is performed in a chamber, immune to ocean currents and marine animals. The warm, dry habitat is well illuminated and has its own environmental control system (ECS). 2) Good Quality Welds - This method has ability to produce welds of quality comparable to open air welds because water is no longer present to quench the weld and H2 level is much lower than wet welds. 3) Surface Monitoring - Joint preparation, pipe alignment, NDT inspection, etc. are monitored visually. 4) Non-Destructive Testing (NDT) - NDT is also facilitated by the dry habitat environment.
- DISADVANTAGES 1) The habitat welding requires large quantities of complex equipment and much support equipment on the surface. The chamber is extremely complex. 2) Cost of habitat welding is extremely high and increases with depth. Work depth has an effect on habitat welding. 3) At greater depths, the arc constricts and corresponding higher voltages are required. 4) The process is costly - a $ 80000 charge for a single weld job. One cannot use the same chamber for another job, if itis a different one.
- WET WELDING • Simply means that job is performed directly in the water • It involves using special rod and is similar to the process inordinary air welding
- PRINCIPLE OF OPERATION • The process of underwater wet welding takes in the followingmanner: • The work to be welded is connected to one side of an electric circuit,and a metal electrode to the other side. • These two parts of the circuit are brought together, and then separated slightly. The electric current jumps the gap and causes asustained spark (arc), which melts the bare metal, forming a weldpool. • At the same time, the top of electrode melts, and metal droplets areprojected into the weld pool. During this operation, the flux coveringthe electrode melts to provide a shielding gas, which is used tostabilize the arc column and shield the transfer metal. • The arc burns in a cavity formed inside the flux covering, which isdesigned to burn slower than the metal barrel of the electrode.
- WET WELDING
- PARAMETERS • Power supply : DC 300 OR 400 AMP • Polarity : straight polarity
- EFFECT OF WET ENVIROMENT • WATER = HYDROGEN + OXYGEN • Dissolve in weld pool • Solubility decreases and then comes out = porosity • Oxygen as solid , liquid inclusions or gases • Hydrogen combines with oxygen forming vapor. V-groove wet weld deposited at 100 m depth (a) and its radiographic image
- Formation of Hydrogen • Once the welding circuit is completed by striking an arc, the heat of the arc is sufficient to vaporise the surrounding water. Hence, the arc is surrounded by a vapor shield. However, reaction with the molten metal influences the composition of this vapor and it comprises of about 70% hydrogen, 25% carbon dioxide and 5% carbon monoxide. • The risk of hydrogen induced cracking increases as welding depth increases in water (sea/ocean).
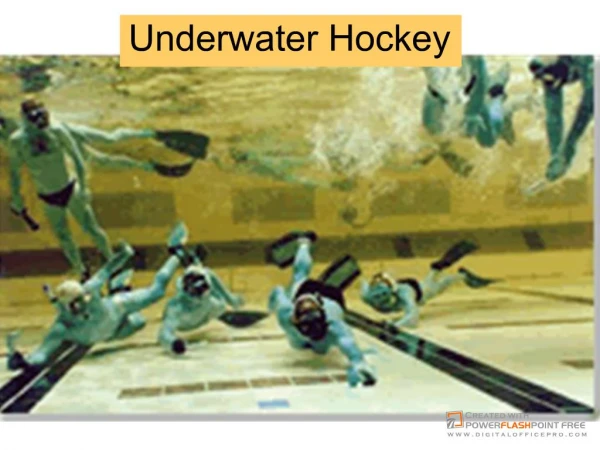
Underwater Hockey
Underwater Hockey The contents of this presentation are based on real information. Undewater hockey is a sport currently being played in many countries around the world.
2.81k views • 11 slides
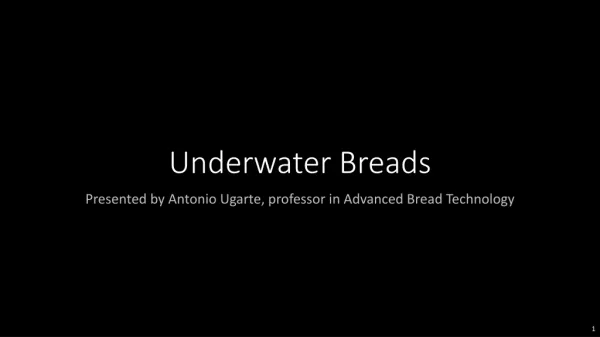
Underwater Breads
Underwater Breads. Presented by Antonio Ugarte, professor in Advanced Bread Technology. Are you afraid of making bread without yeast?. History of Breads.
426 views • 10 slides
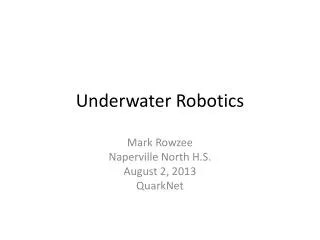
Underwater Robotics
Underwater Robotics. Mark Rowzee Naperville North H.S. August 2, 2013 QuarkNet. What is ‘underwater robotics’?. Tethered control of a student-designed, student-built, remotely-operated vehicle (ROV) Camera-eye view operation
2.03k views • 20 slides
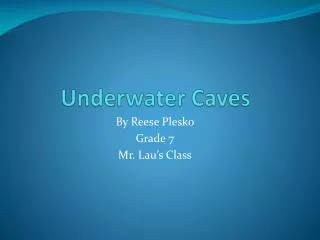
Underwater Caves
Underwater Caves. By Reese Plesko Grade 7 Mr. Lau’s Class. Underwater Caves.
352 views • 14 slides
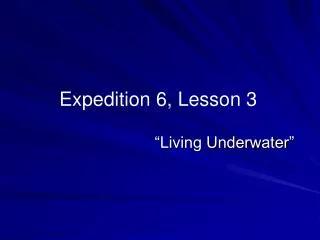
“Living Underwater”
“Living Underwater”. Expedition 6, Lesson 3. device. Marc is trying to invent a device that makes instant ice cubes. A tool that does a certain job. gear. The fishing gear we’ll use on our trip will fit into the back of the truck. The tools needed for an activity. central.
216 views • 10 slides
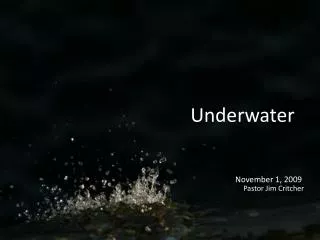
Underwater
Underwater. November 1, 2009. Pastor Jim Critcher. 2Kings 6:1-7
648 views • 28 slides
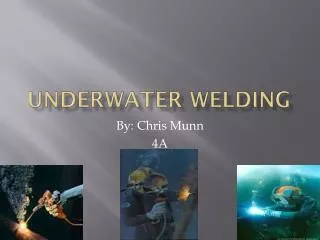
Underwater Welding
Underwater Welding. By: Chris Munn 4A. Description.
292 views • 7 slides
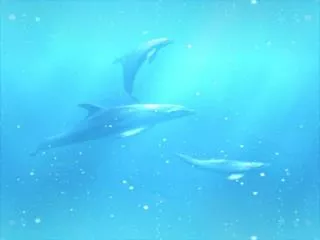
Underwater Photographs
446 views • 31 slides
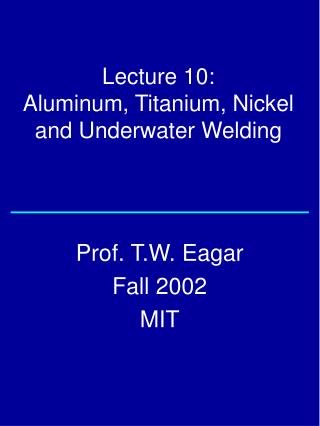
Lecture 10: Aluminum, Titanium, Nickel and Underwater Welding
Lecture 10: Aluminum, Titanium, Nickel and Underwater Welding. Prof. T.W. Eagar Fall 2002 MIT. Design of Joints that are Half Strength of Base Metal (ie. for heat treated aluminum). weld design is more critical generally more weld metal required which makes joining more expensive.
337 views • 13 slides
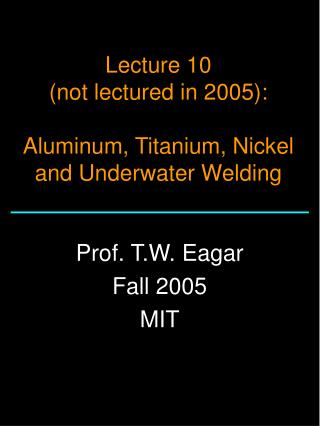
Lecture 10 (not lectured in 2005): Aluminum, Titanium, Nickel and Underwater Welding
Lecture 10 (not lectured in 2005): Aluminum, Titanium, Nickel and Underwater Welding. Prof. T.W. Eagar Fall 2005 MIT. Design of Joints that are Half Strength of Base Metal (ie. for heat treated aluminum). weld design is more critical
227 views • 13 slides
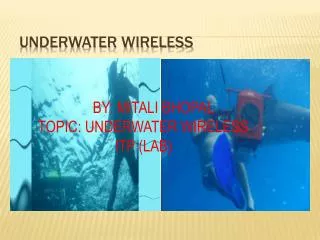
UNDERWATER WIRELESS
UNDERWATER WIRELESS. BY: MITALI BHOPAL TOPIC: UNDERWATER WIRELESS ITP (LAB). We can use Underwater S ensor Networks (UWSN): • Ocean Sampling Networks • Environmental Monitoring • Undersea Explorations • Disaster Prevention
543 views • 12 slides
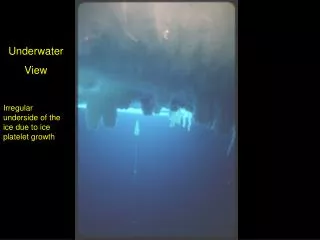
Underwater View
Underwater View. Irregular underside of the ice due to ice platelet growth. Under Ice Diving McMurdo Sound. Kevin Hoefling. Sea Urchin holding a piece of algae shrouded with platelet ice. Isopod grazing on ice crystals Body fluids Isosmotic to Seawater
466 views • 27 slides